How to develop full-color epaper?
Size | |
Display Technology | |
Resolution | |
Interface | |
Luminance | |
Outline Dimension | |
Active Area | |
Viewing Angle | |
Model Name | |
Operation Tmperature | |
Storage Temperature | |
Shape Type |
At the MIT Media Lab in 1997, inspired by professor Joseph Jacobson, two students J. D. Albert and Barrett Comiskey Create an e-ink screen.
E-paper has been viewed as magical from the beginning.
It’s eye-friendly and can be seen clearly even outdoors in bright sunlight, where other portable displays become unreadable in sunlight. E-paper lasts for weeks before needing to be recharged, whereas phones with other displays barely last a day. However, the limitations of electronic paper are also obvious-pictures can only be displayed in black and white. In a world that hasn’t seen a monochrome display in a long time—black-and-white televisions were replaced by color TVs as early as the 1960s, and the shift to computer monitors came in the late 1980s—monochrome displays are unquestionable. Both corny and fun.
So, from the time the underlying technology behind e-paper, e-ink, was first developed, a big question has loomed over e-paper, and has become increasingly prominent with the release of the Kindle reader: When will we see this magic? The display shows vivid colors? It’s not like researchers haven’t tried. E-ink researchers at universities, corporate labs, and startups around the world have been pursuing color e-paper for years. They developed some early products targeting shelf labels in brick-and-mortar retail stores and also for signage. But these early products merely added a color (red or yellow) to a black-and-white display, and that wasn’t what anyone thought of as a full-color display. More than a decade after the first Kindle reader was released, and more than two decades after the invention of e-paper, full-color e-paper still has not entered the consumer market.
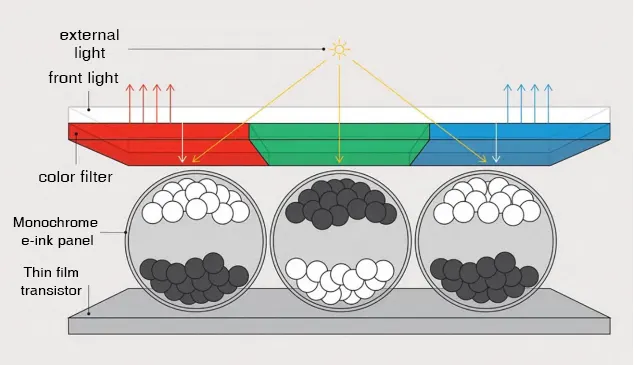
Why did the transition from black and white to color electronic paper take so long? Over the years, researchers have tried a variety of approaches, some with technologies derived from more traditional displays, and others with unique designs that evolved from the original e-paper. Qualcomm, for example, spent billions of dollars researching a method inspired by butterfly wings. Overall, color e-paper’s road to success may have been a bit winding, but it’s still a classic technological triumph story.
Today, E Ink’s full-color electronic paper is in the hands of consumers, appearing on products including e-readers, smartphones and note-taking devices. There are more than a dozen manufacturers producing these products, including Guoyue V5 color ink screen notebook, Hisense A5C color ink screen reading phone, Aragonite Boox Poke 2 color ink screen reader and PocketBook color ink screen reader, etc. Among the full-color electronic paper products announced so far, in addition to the technology of electronic ink companies, there is only one plasma display screen (DES) launched by China’s Dalian Jiaxian Company. As of this writing, no devices using DES technology have yet been shipped to consumers, but several reporters have received samples, and two Kickstarter companies are targeting products that will use DES displays.
The challenge with color e-paper stems from the nature of the technology. Black and white e-ink is a straightforward fusion of chemistry, physics, and electronics that accomplishes nearly the same thing as traditional ink and paper. E-ink’s products are made of microcapsules containing negatively charged black particles and positively charged white particles (the same pigments used in today’s printing industry) floating in a clear liquid. Each microcapsule is about the same thickness as a human hair.
To create an e-paper display, researchers first create the e-ink, which is then coated on a plastic substrate to a thickness of about 25 to 100 microns, depending on the type of product it is intended for. A roll of overlay film is then cut into the desired display size, and thin film transistors are added to create electrodes above and below the ink layer, sandwiched between protective sheets if possible. If so, a touch panel or front light will be added.
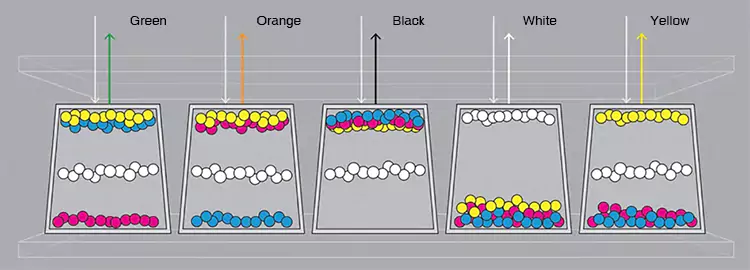
To create an image, an e-paper device applies different voltages to top and bottom electrodes, creating an electric field. The top voltage is close to zero and the bottom voltage varies between -15 volts, 0 volts and 15 volts. Each time the image on the display needs to change, a specific sequence of voltages is applied to the underlying electrodes, driving the particles from their previous position to the position needed to display the correct color for the new image. This image change usually takes less than half a second.
Let the white particles come to the top of the display, creating a “paper” look. Black particles create an “ink” appearance. But particles don’t have to be at the top or bottom. When we stop generating the electric field, the particles stop in their tracks. This means that we can create a mixture of black particles and white particles near the top layer of the display – which appears as grayscale.
The software that determines how long and how much voltage to apply the electric field to each electrode is complex. The specific choice depends on the color previously displayed at that pixel. For example, if a black pixel in one image remains black in the next image, there is no need to apply a voltage to that pixel. We also have to be careful with color transitions. We don’t want the previous image to linger, but we also don’t want a sudden shift in color that causes the display to flicker. These are just some of the factors to consider when designing the algorithm (called a waveform, which we use to determine the sequence of voltages). This part of design work is both a science and an art.
Including color into the equation greatly complicates the waveform. Given that an electric field produces either a positive voltage or a negative voltage, the colors black and white are simple binary opposites. The binary opposition approach cannot be adapted to full-color electronic paper. We need some completely new approaches.
We began exploring options in the early 2000s. One of the first color e-paper products we launched commercially in 2010 used color filters. Color filters are arrays of squares printed on a layer of glass that is placed on top of a standard layer of black and white ink. When we apply a voltage to move the white particles to a selected location on the surface, the light passes through the red, green or blue filter above and is reflected back into the viewer’s eyes. It’s an obvious approach: all the colors humans can see are produced by mixing red, green, and blue light. For this reason, most common display technologies today, such as LCD and OLED, use RGB emitters or color filters.
We named this product “Electronic Ink Triton Screen”. Although electronic textbooks using the technology were launched at the time, the main lesson this experiment taught us was what kind of technology would not work in the consumer market. For users accustomed to the high resolution of tablets or paper magazines, the resolution of this display is simply too low and the colors are not bright enough.
The problem with the lack of bright colors stems from the fact that, unlike backlit LCDs or direct-emission OLED displays, E-Ink’s Ink screens are fully reflective. That is, light from an external light source passes through the transparent protective layer, hits the ink layer, and is reflected back into the viewer’s eyes. This arrangement is great for outdoor use, as the reflective display will be enhanced rather than dimmed by bright sunlight. Such displays are also good for eye comfort because they don’t shine bright light directly into the user’s eyes. But in reflective display systems, each layer between the ink layer and the eye absorbs or scatters away some light. It turns out that adding a color filter layer makes the display much dimmer.
In addition, color filters are used to separate single-color pixels into three colored pixels, which lowers the overall resolution. The original resolution of the display screen was 300 pixels per inch (1 inch is approximately 2.54 cm). After adding a three-color filter, the resolution was reduced to 100 pixels per inch. Not a big deal for a 32-inch display used as a sign—the pixel size can be made larger, and the giant letters don’t require high resolution. But for tiny fonts and line drawings on handheld devices, this is a real problem.
We have researchers who conceived the filter display, and other researchers in the company’s labs are looking at a different approach that uses multi-pigmentation and doesn’t rely on color filters. However, that approach requires more complex chemical and mechanical mechanisms.
Multi-color e-paper shares the same basic principles as previous monochrome e-paper. However, whereas monochrome e-paper only has two types of particles, multi-color e-paper now uses three or four types of particles, depending on the color selected for a specific application.
We need to make these particles respond uniquely to electric fields, rather than simply being attracted or repelled. We’ve made some changes to the ink particles so they can be sorted better. We make the ink particles vary in size – larger particles generally move more slowly through the liquid than smaller particles. We differentiate the voltage applied to the particles, taking advantage of the fact that voltage changes are more analog than digital. That is, the voltage can be a very strong positive voltage, a slightly positive voltage, a very strong negative voltage, or a slightly negative voltage. And there are many degrees between them.
Once we separate the particles, we have to apply a waveform. Instead of just sending one set of particles into the top layer and another set into the bottom layer, we push and pull them to create the image. For example, we can push particles of one color to the top and then pull them back slightly so they mix with other particles to create a specific color. Cyan mixes with yellow to create green, while white particles provide a reflective background. The closer one type of particle is to the surface, the greater the concentration of that color in the mix.
We also changed the shape of the pigment container from a sphere to a trapezoid, which gave us better control over the vertical position of the particles. We call these containers microcups.
For systems with three types of particles (called e-ink Spectra screens on the market today and mainly used in electronic shelf labels), we put black and white red or black and white yellow pigments into each microcup. In 2021, we added a fourth pigment particle to the system: our new generation uses black, white, red and yellow particles. This produces extremely saturated, high-contrast colors, however, these four colors cannot be mixed to produce a full-color image. The technology was first introduced in 2013 for electronic shelf labels in the retail industry. Several companies have used E-Ink’s displays to create millions of electronic shelf labels that are shipped around the world for use in Best Buy, Macy’s and Walmart stores. There are also similar electrophoretic shelf labels using displays produced by China Oriental Kemai Company, and the products have already been on the market.
E Ink’s true full-color e-paper system is called Advanced Color e-Paper (ACeP). We also use four pigment particles in this e-paper, but we abandon the black particles and rely on white, cyan, and magenta. and yellow particles, the four colors used in inkjet printers. By stopping the particles at different levels, we can use them to create up to 50,000 colors. The resulting display renders colors like those found in newspapers or even watercolor paintings.
E-Ink launched advanced color e-paper in 2016 under the name E-Ink Gallery.
This display is once again unsuitable for consumer devices due to its low refresh rate. Plus, it’s a reflective display with no backlight, making its colors too muted for consumers accustomed to bright displays on smartphones and tablets. Currently, it is mainly used in Asia for retail signage.
We realized that our color ink display still hadn’t hit the sweet spot in the consumer market, so the company’s R&D team went back and looked again at Triton screens, which are systems that use RGB color filters. What systems work and what systems don’t?
Will the changes we make finally lead to a color e-reader that consumers want? We know that filters reduce brightness. We’re fairly confident that by moving the filter closer to the e-ink layer, the loss in brightness can be significantly reduced. We also want to increase the resolution of the display, which means using a finer array of color filters.
In order to obtain a resolution more in line with consumer habits, we need to shoot at least 200 pixels per square inch (1 square inch is approximately 6.5 square centimeters). That’s about twice the density we were able to achieve with our first Triton displays.
Compared to the complexity of controlling pigment particles with different voltages (as we did when developing ACeP), you might think this would be easy to do. But it turns out that this requires a new technology that prints color filters on glass substrates.
We previously printed translucent red, green and blue inks on glass to create filters.
But this glass is an overlay. So we decided to print directly on the plastic film that houses the top electrodes, adding this step towards the end of the packaging process for our display modules. This arrangement puts the filter as close as possible to the e-ink layer. This also allows us to increase the resolution because the filters can now be aligned with the display pixels more precisely than would be possible with an extra layer of panels.
We found the type of printer we needed in the German company Plastic Logic, which has been a partner of E-Ink since its early days. However, the press was intended for use in research and development laboratories, not for mass production. The process in which it is used must be adapted to operate in a different production-ready machine.
We also need to come up with new printing patterns for color filters. That is the actual shape and arrangement of the red, blue and green filter arrays. We discovered through our earlier work developing the Triton display that printing the filter array as a simple grid of squares was not the best solution because the pattern would be visible during certain image transitions. And so the search for the perfect pattern continued. We went through many iterations, taking into account the angle at which light hits the display, as this angle can easily change the colors a viewer sees. We evaluated grids, straight lines, long lines, and many other patterns before settling on a short line pattern.
Because this is a reflective display, the more light that hits the display, the brighter it becomes. The research team decided to add a front light to the display (an aspect not used in the Triton display), working to ensure that the light hits the ink layer at an angle to maximize reflectivity. Of course, using a front light will increase energy consumption, but in this case it is worth it.
As a result, E-Ink’s new color ink screen technology “E-Ink Kaleido” has more saturated colors and better contrast than Triton screens. Finally, a full-color e-ink display is ready for consumer products.
The first batch of official Kaleido displays will roll off the production line in the second half of 2019. Soon after, we started shipping goods to customers. You can currently see this technology in products such as Hisense A5C color ink screen reading phone, iFlytek C1 reader and PocketBook color ink screen reader, all of which will be launched in 2020. Year. The second generation of Kaleido displays, called Kaleido Plus, began shipping to manufacturers in early 2021, with related products from companies like Aragonite and PocketBook arriving soon after. The second-generation Kaleido display has improved color saturation, thanks to adjustments to the printed pattern and front-light light guide.
We still have some things to do. The ratio of incident light that is reflected back to the user’s eyes is called optical efficiency. The light efficiency of the company’s current products is very good, but it could be better. We continue to work on thin film layers to further reduce the loss of brightness.
We continue to refine the printed patterns, use denser circuits in the electronics beneath the ink layer, and work to improve resolution by switching voltages to move charged particles.
We are also continuing to research filter-free, multi-pigment e-ink technology. We expect to launch a new generation of displays for signage soon that will feature more vibrant colors and faster page updates.
When researchers at Electronic Ink set out to explore color electronic ink in the early 2000s, they thought they would have results within a few years, given their expertise in electronic paper technology. After all, it only took ten years for black and white electronic paper to go from concept to commercialization. As it turns out, the road to full-color ebooks is much longer. But, just like Dorothy in The Wizard of Oz, we eventually make it to the other side of the rainbow.